
19 Apr Best Practices for Industrial Construction Services

SJEC industrial construction project.
Industrial construction encompasses creating facilities such as factories, warehouses, and power plants, which are essential for various industries.
This guide by Sheng Jian Engineering and Construction (SJEC) offers practical insights for informed decisions and efficient project management related to industrial construction, allowing you to stay ahead of the competition.
Throughout this guide, we will explore the intricacies of industrial construction, discussing the common difficulties faced and the strategies employed by SJEC to overcome them.
By sharing our experiences and best practices, we aim to empower you to navigate the complexities of industrial construction with confidence and achieve successful project outcomes.
The Basics of Industrial Construction
What is industrial construction?

Industrial construction is the art of shaping dreams into reality, transforming vast expanses of land into bustling hubs of innovation and progress.
It’s the symphony of steel and concrete, where every beam, every bolt, and every brick is a testament to human ingenuity and perseverance.
It’s not just about erecting structures; it’s about creating a legacy that withstands the test of time, a testament to our commitment to excellence and our drive to build a better tomorrow.
Join us as we delve into the world of industrial construction, where challenges are opportunities, and every project is a canvas for greatness.
Industrial construction isn’t just about building structures; it’s about building bridges to a brighter future. Take the Hong Kong-Zhuhai-Macau Bridge, for example. This marvel of engineering didn’t just reduce travel times; it transformed businesses and entire industries.
Imagine being a logistics company that’s suddenly able to make more deliveries in less time, saving on fuel and increasing efficiency. Now, multiply that impact across every business using the bridge. That’s the power of industrial construction on a grand scale.
From skyscrapers that pierce the clouds to futuristic robot-run warehouses and sustainable cities like Songdo, South Korea, industrial construction enables us to turn ambitious visions into reality.
It’s about unlocking new possibilities and creating a legacy that shapes our world for generations to come. So, if you have a vision for a better tomorrow, remember, industrial construction is the bridge that can make it a reality.
Types of industrial buildings

Discover the world of industrial construction, where innovation meets inspiration. From towering skyscrapers to cutting-edge factories, each structure tells a story of creativity and progress. Join us as we explore the diverse types of industrial buildings that shape our modern world:
Types of Buildings | Details |
---|---|
Warehouses | |
Factories | |
Power Plants | |
Refineries | |
Key Takeaway: Your goals dictate the design. A skilled industrial contractor will transform your vision into a purpose-built reality.
Types of industrial construction services
Building your vision takes more than concrete and steel. Industrial construction is a symphony of specialized services, each vital in bringing your project to life. Let’s dive into some of the key players:

Industrial Construction Best Practices and Considerations

SJEC current ongoing industrial construction project.
Think of your industrial project as a high-performance engine.
Sure, it needs the right parts, but for peak efficiency, those parts need to work together perfectly. Best practices are your fine-tuning guide, ensuring everything from planning to handover runs like a well-oiled machine.
The Importance of Meticulous Planning
In industrial construction, there’s no room for “winging it.” Meticulous planning is your competitive edge. Here’s why:
- Cost Control: Think of it like a financial shield. Detailed plans mean accurate budgets. You’ll know exactly where your money goes, from those high-tech ventilation systems to specialized flooring. Ultimately, proper planning lowers the risk of project delays and exceeding your budget.
- Timeline Mastery: Break down the big build into smaller, achievable steps. Plan when permits are needed and when materials should arrive – every little detail matters. This kind of foresight helps you stay on schedule and avoid those frustrating (and expensive) delays.
- Optimized Resources: The right tools, the right people, the right materials, all at the right time. Planning takes the guesswork out of logistics. You won’t have skilled workers sitting idle because a crucial part is stuck in a shipping backlog.
Remember, meticulous planning isn’t just paperwork, it’s the foundation of a successful build. It saves you money, time, and many headaches.
Clear Communication and Collaboration
In construction, talk isn’t cheap – it’s priceless.
Crystal-clear communication between everyone involved is the grease that keeps your project’s wheels turning. Here’s why it matters:
- Clarity = Efficiency: Ambiguity is the enemy of progress. Detailed reports, regular check-ins, and sharing updates with all stakeholders keep everyone on the same page. Think of it like this: Clear directions save time, and in construction, time is money.
- Risk Mitigation: Open communication channels build trust, empowering teams to raise red flags early. Maybe a potential supply chain issue is looming, or there’s a safety concern on-site. Flagging these things early allows for quick solutions, minimizing the chance of a minor problem snowballing into a major project derailment.
- Shared Vision: Your industrial facility isn’t being built in isolation. Architects, engineers, tradespeople, safety inspectors – everyone plays a vital role. Consistent communication ensures that all these moving parts work harmoniously towards the same goal: bringing your vision to life.
As above, effective communication isn’t a “nice to have” in industrial construction, it’s how you achieve on-time, on-budget success.
Embracing Technology and Safety
Industrial construction isn’t about clinging to old ways. It’s about harnessing the latest tools and prioritizing safety every step of the way. Here’s how this forward-thinking mindset sets your project up for success:
- AutoCAD Virtual Blueprint: AutoCAD is essential in industrial construction for its design and drafting capabilities. It allows for detailed 2D and 3D modeling, visualization of final products, precision in measurements, collaboration among team members, detailed documentation creation, and easy modification and updates to designs.
- Smart Safety: Protecting your people isn’t just the right thing to do; it’s smart business. Wearable tech that warns about hazards, digital safety training, and even sensors that monitor dangerous gasses in real time aren’t just gadgets; they’re safeguards. And a safe project stays on schedule.
- Data-Driven Decisions: Forget the guesswork. Sensors on the site can track everything from material usage to air quality. This data isn’t just numbers; it’s power. Analyzing it can help you pinpoint areas to save time, cut costs, or even improve worker safety procedures.
Tech and safety go hand in hand in modern industrial construction. This kind of investment doesn’t just build better facilities; it creates a better future for your project and for the people bringing it to life.
Sustainable Construction
In industrial construction, going green isn’t just about doing the right thing – it’s about doing things smarter. Here’s why sustainability matters to your bottom line:
- Cost Savings Over Time: Sure, those eco-friendly materials might have a slightly higher upfront cost, but they pay for themselves over time. Think durable materials that last longer, energy-efficient systems that cut your utility bills, and designs that minimize waste.
Did you know buildings consume roughly 40% of the world’s operational energy use? Choosing sustainable options puts a dent in that number and in your operational costs, as well as attracting sustainability-focused clients.
- Optimized Resource Use: Sustainability isn’t just about what you use but how you use it. Smart design optimizes everything – from material efficiency to minimizing construction waste. Every scrap of material that doesn’t end up in a landfill saves you money.
- Market Appeal: Today’s clients aren’t just looking for a building, they’re looking for a partner that shares their values. A sustainable project shows you’re invested in the future – and that can attract lucrative, forward-thinking businesses.
- Competitive Edge: Be the one setting the standard, not scrambling to catch up. Sustainable construction is the industry’s future. Embrace it now, and you’ll be miles ahead of competitors who adapt slowly.
Sustainable construction isn’t about sacrifice; it’s about smarter building. It makes your project more efficient, resilient, and attractive to the growing market of clients who care about the planet.
Managing Complexities in Industrial Construction Projects
Sustainable construction isn’t about sacrifice; it’s about smarter building. It makes your project more efficient, resilient, and attractive to the growing market of clients who care about the planet.
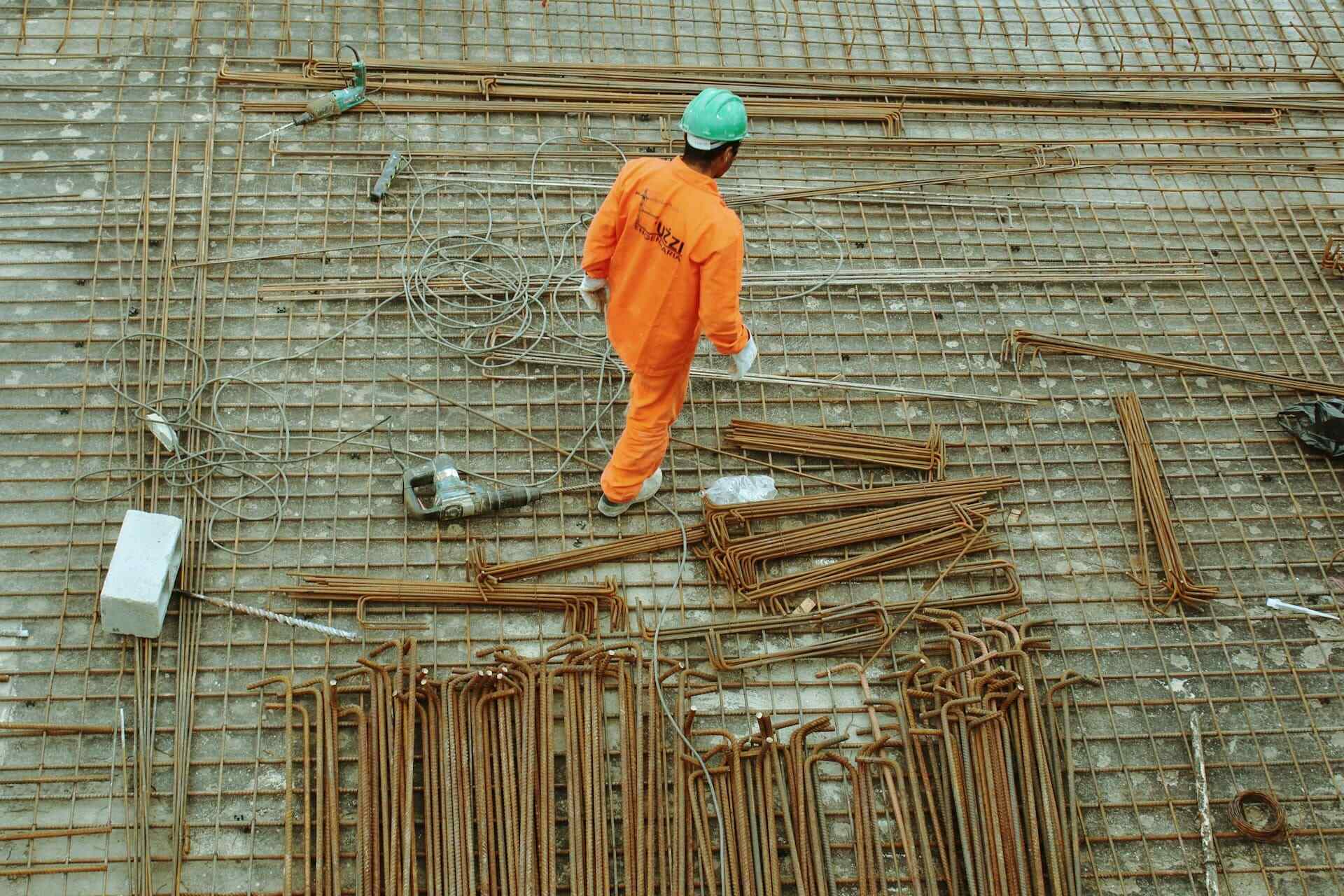
Let’s be real: even the most meticulously planned industrial project can hit a snag. But the difference between a headache and a full-blown disaster is preparedness. Here’s how to think like a seasoned project manager and keep those complexities under control:
Proactive Risk Identification
Never assume smooth sailing.
Smart project management is about identifying potential problems before they become real ones. Thoroughly analyze your site, understanding everything from the soil conditions to those pesky weather patterns that could disrupt your schedule.
Know your local labor market – are there enough skilled workers available?
Research your supply chain – are there any red flags about material shortages?
This kind of foresight isn’t just about avoiding headaches but protecting your investment.
Unforeseen issues are inevitable, but a strategic, risk-aware approach transforms them from crippling problems into manageable bumps in the road.
Contingency Planning
Hope for the best, and plan for the rest. That’s the mantra of successful industrial construction. Contingency plans are your safety net, protecting your project from those inevitable curveballs. Here’s why they matter:
- Mitigating Impact: No one likes surprises, especially the expensive kind. A contingency budget (think of it like an emergency fund for your project) absorbs unforeseen costs. Maybe that specialized material is suddenly backordered, or a key piece of equipment needs emergency repairs. Having a cushion built-in makes these hiccups less disruptive.
- Safeguard Operations: Safety is always the first priority. Contingency plans don’t just protect your budget; they protect your people. Plan for potential hazards, have emergency procedures in place and make sure your equipment is rigorously maintained. Every incident prevented is a win for your project.
- Managing Change: The only constant in construction is change. Clients change their minds, regulations get updated, even something as simple as bad weather can disrupt plans. Contingency planning makes your project adaptable. Have a system for quickly evaluating change requests and minimizing their impact on your schedule or budget.
Contingency planning isn’t about being negative; it’s about being realistic. It allows you to navigate even the most challenging situations and still deliver the kind of facility you promised.
Change Management
In industrial construction, the best-laid plans sometimes need tweaking. Change isn’t a planning failure; it’s part of the process. The key is to handle it with agility, not panic. Here’s how to turn those curveballs into opportunities:
- Effective Communication: Nobody likes being blindsided in construction. Open and transparent communication about any potential changes (and their impact) is crucial for keeping everyone on track. Clear updates minimize those panicked phone calls and rushed decisions – which is when costly mistakes happen.
- Flexible Planning: Think of your initial plan as a roadmap, not a railroad track. Build some wiggle room into your schedules and budgets. This doesn’t mean being sloppy, but it means being realistic. When changes do occur, you’ll be able to adapt without everything grinding to a halt.
- Team Problem-Solving: Your crew on the ground sees challenges first-hand. Encourage them to offer solutions, not just complaints. This collaborative approach means you leverage the expertise of everyone involved and fosters a sense of shared responsibility for overcoming obstacles.
Change in industrial construction is inevitable. A proactive, solutions-focused approach lets you gracefully navigate these adjustments, protecting your timeline and keeping your ambitious vision on track.
Challenges in Industrial Construction and Solutions

Even the most ambitious industrial construction projects face hurdles. But overcoming these challenges is precisely what separates good projects from great ones. Let’s look at a common pain point and how to take it head-on:
Cost Control and Budget Management
No one wants to see their budget turn into a money pit. That’s why cost control isn’t just about penny-pinching; it’s about strategic spending from day one. Here’s how to protect your investment:
- Precision Budgeting: Ditch the guesswork. Advanced estimating software and experienced project managers can give accurate cost projections. This way, you’re not starting a project blindfolded.
- Financial Transparency: Don’t wait until the bills pile up. Regular, detailed financial reports are your early warning system. They allow you to spot potential overruns and adjust before they become major budget disasters.
- Strategic Value Engineering: Find smarter ways to achieve the same results. Think alternative materials, streamlined processes, and even tweaking the design – all without compromising the core function of your facility. It’s about maximizing value, not cutting corners.
Uncontrolled costs can sink even the most exciting project. Proactive, data-driven financial management keeps your budget on track and helps you deliver a facility that exceeds expectations (without breaking the bank).
Compliance with Regulations
In industrial construction, red tape isn’t optional – it’s the rulebook. But navigating those regulations doesn’t have to be a nightmare. A proactive approach ensures your project stays on track and keeps you out of hot water. Here’s your compliance checklist:
- Dedicated Compliance Officer: Large projects need a point person for all things regulatory. This expert tracks constantly evolving rules, integrates compliance into planning, and keeps everyone informed. Think of them as your shield against costly fines and delays.
- Partnering with Experts: Don’t try to DIY complex regulations. Environmental consultants, zoning specialists, even lawyers with a focus on construction – they know the legal nitty-gritty better than anyone. Their expertise is your insurance policy against significant compliance missteps.
- Rigorous Documentation: Prove you’re doing things by the book. Maintain detailed records of permits, inspections, safety training, and other relevant paperwork. This isn’t just about bureaucracy, it’s about protecting yourself if a compliance issue ever arises.
All this in mind, cutting corners on regulations can derail your project faster than you think. By prioritizing compliance from the start, you avoid costly delays, protect your reputation, and, most importantly, keep everyone safe.
Securing Skilled Labor
Your dream facility won’t build itself.
In today’s construction industry, finding the right people is as important as finding the right materials. Here’s how to make sure your project has the skilled hands to bring it to life:
- Investing in Training: Don’t wait for skilled workers to appear magically. Grow your own talent pool with apprenticeship programs, partnerships with trade schools, and even internal upskilling initiatives. Did you know companies that invest in training are likely to achieve a higher profit margin? It’s not just about filling jobs, it’s about building a more robust workforce for the future.
- Competitive Incentives: Paychecks matter, but so does quality of life. Attract the best by offering benefits that go beyond the bare minimum. Think healthcare, retirement savings, and even flexible working arrangements. This shows you value your workers, not just their labor.
- Building a Positive Culture: Happy workers are productive workers Foster a workplace where people feel respected, safe, and like they have opportunities to grow. Reputation matters – skilled workers want to work for a company they can be proud of.
The global skilled labor shortage is a reality, but it doesn’t have to derail your project. Proactive workforce strategies make you the employer of choice, attracting top talent and ensuring your timeline stays on track.
Sustainability Concerns

Industrial construction has a responsibility to the planet. But going green isn’t just about doing the right thing, it’s about doing things smarter. Here’s why sustainability should be front and center in your project:
- Beyond the Initial Investment: Sustainable solutions, like energy-efficient systems or durable materials, might have a slightly higher upfront cost. But think long-term: they slash energy bills, reduce maintenance, and last longer.
- Market Appeal: Today’s clients aren’t just looking for a functional building; they’re looking for a partner that shares their commitment to sustainability. By showcasing your green building practices, you attract a whole new market of forward-thinking businesses.
- Long-term Savings: Sustainability often delivers unexpectedly high returns, as much as 20% life cycle savings of total construction costs. Therefore, a green roof might seem expensive, but did you know it can double the lifespan of a conventional roof? This proactive approach means less money down the road on repairs or replacements.
In the past, sustainability might have seemed like a sacrifice, but today it’s an investment. It attracts clients, prepares you for future regulations, and ultimately delivers a facility that’s both better for the planet and for your bottom line.
Ensuring Successful Industrial Construction Projects
Building a successful industrial facility isn’t about luck; it’s about strategic partnerships. Choosing the right contractor has a direct impact on the outcome of your project. Here’s why experience matters:
Partnering with an Experienced Contractor
Your dream industrial facility deserves the best possible builders. Choose wisely, and your contractor won’t just build your project, they’ll help you build a brighter future. Look for these signs of a true partner:
- Industry Expertise: There’s no substitute for experience. A contractor with deep knowledge of your specific industry understands your needs and speaks your language. They know the regulations, the common hurdles, and the best practices to get things done efficiently.
- Proven Track Record: Don’t be their guinea pig! Seek contractors with successful projects under their belt. Look at case studies, read those reviews – find proof that they deliver on promises, both on time and on budget.
- Safety Focus: Accidents aren’t just a human cost; they’re a massive drain on your resources. Prioritize contractors with a strong safety culture – it means they put their people first, and that’s the kind of company that keeps your project running smoothly.
- Robust Network: Access to the right materials, the right specialists, the right skills – this is what separates good contractors from great ones. A well-established network means fewer delays due to supply chain issues or a struggle to find the right talent.
Building a high-performance industrial facility is a team effort. Choose an experienced contractor and you’re not just buying construction services, you’re investing in a partnership that ensures your vision becomes a successful reality.
Setting Clear Project Goals and Metrics
Forget generic ambitions. In industrial construction, a successful project starts with a laser-sharp definition of what “success” means for you. This isn’t just about the end result; it’s about setting a clear course for the entire journey.
Here’s why it matters:
- Define Success Criteria: Go beyond the blueprints. Is top priority maximizing output? Creating the most sustainable facility possible? Building to the highest safety standards? Clearly defining your goals aligns every decision towards achieving them.
- Establish KPIs: Data is your ally. Key Performance Indicators (KPIs) track progress against your goals. Whether it’s tracking on-time completion, staying within budget, or monitoring safety incidents, these metrics keep your project on track.
- Set Milestones: Break big goals into achievable steps. This keeps projects moving, allows for early identification of potential issues, and provides much-needed moments of celebration as your facility takes shape.
Setting clear goals isn’t a paperwork exercise; it’s how you build a successful team. When everyone understands the shared vision, they’re empowered to contribute their expertise, collaborate effectively, and ultimately take pride in delivering a facility that surpasses your expectations.
Post-Project Evaluation and Continuous Improvement
The true value of your industrial construction project isn’t just about the first day it’s operational. It’s about what comes next – continuous learning and continuous improvement. Here’s why this final stage is just as important as the first:
- Thorough Analysis: Data doesn’t lie. Compare your initial goals and KPIs to the real-world performance of your facility. Are you meeting production targets? Hitting those energy efficiency targets? This honest, data-driven analysis reveals what’s working and what might need tweaking.
- Lessons Learned: Every project is a learning opportunity. Document both the successes and the challenges. What aspects of construction went exceptionally smoothly? Were there any unexpected hurdles? This kind of documentation turns experience into expertise.
- Continuous Improvement: Don’t settle for “good enough.” Use the knowledge gained from your project to improve every aspect – from safety protocols to efficiency on the factory floor! Choose a contractor who is also invested in this process – it means they’re as dedicated to the future of your facility as its initial build.
In industrial construction, the finish line is a new starting line.
Post-project evaluation isn’t just about fixing what went wrong – it’s about making what’s already good even better. This approach ensures your facility stays competitive and your investment continues to pay dividends for years to come.
SJEC’s Excellence in Industrial Construction Services
Over the past two decades, SJEC has earned a strong reputation for its exceptional work in factory construction, plant renovation, mechanical & equipment fabrication, and installation across various industries.
With extensive experience and a dedication to excellence, SJEC consistently exceeds client expectations, setting the standard for quality and innovation in the field.
Below are some examples of our successful projects, showcasing our expertise in delivering high-quality industrial construction and factory building services.

Storage Shed in Perlis by SJEC.
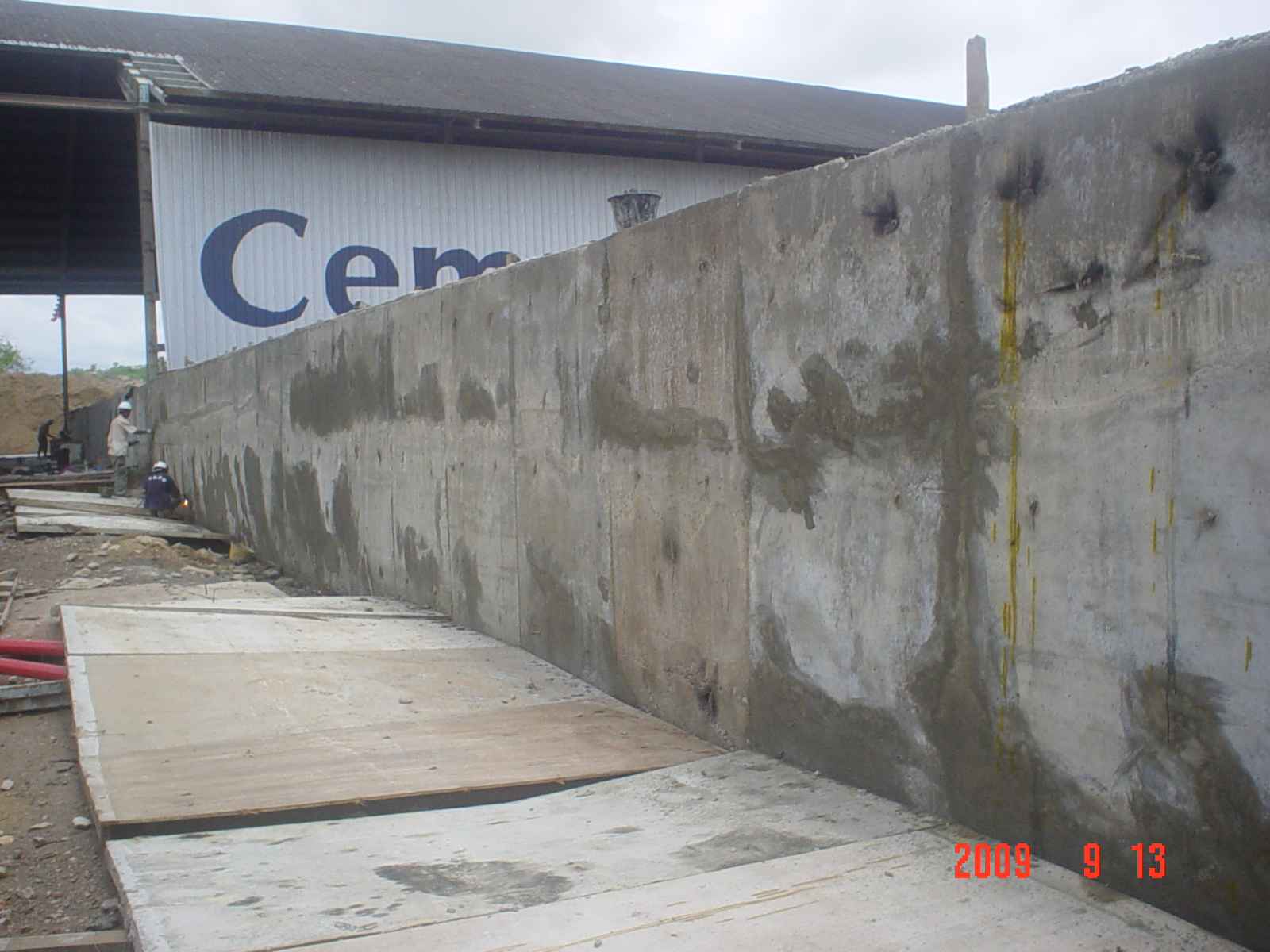
Retaining Wall Slab in Perlis by SJEC.

Lost World of Tambun Waterslide by SJEC.

Shelter by SJEC.
Closing Thoughts
Industrial construction isn’t just about erecting buildings, it’s about building the future. It’s about creating the infrastructure that fuels progress and enables innovation.
But even the boldest ambition needs the right execution – that’s where a strategic mindset and unwavering commitment to excellence make all the difference.
The principles we’ve discussed – meticulous planning, embracing sustainability, prioritizing safety – are essential.
But success in industrial construction is also about finding the right partner, one who understands your industry, speaks your language, and shares your commitment to building a better future.
That’s where SJEC excels. We’re not just builders, we’re strategic partners. Our experience, track record, and dedication to continuous improvement are the foundation of your project’s success.
Interested in Industrial Construction Services?
If you’re ready to see your vision become a reality, let’s talk. Visit SJEC to learn more about our capabilities and see why clients trust us with their most ambitious projects.
Contact us today for a personalized consultation and see how our expertise can become your competitive edge.
Partner with SJEC and build with confidence.
Sheng Jian Engineering & Construction (SJEC) – Industry Experts
With over two decades of experience, SJEC is a certified expert in industrial construction and factory building. We guarantee first-rate results for every project, leveraging our customized solutions, expertise in complex industrial ventures, and safety-first approach.
Going a step further, we integrate eco-friendly practices into our industrial construction projects. This allows our clients to meet their eco-conscious goals while maintaining operational efficiency.
Here are the type of industrial construction services we provide:
Here are the type of industrial construction services we provide:
- Warehouses
- Material storage sheds
- Industrial Equipment Installation Service
- Production Line Installation Service
We have served a wide array of industries, including:
- Architecture
- Automotive
- Chemical
- HVAC and Electric Industry
- Industrial Construction
- Oil and Gas Industrial
- Oleochem Industrial
- Petrochem Industrial
- Renewable Energy
FAQ
What does industrial construction include?
Industrial construction encompasses the building of facilities such as factories, warehouses, power plants, and other structures used for manufacturing or processing of goods.
How do you plan an industrial project?
Planning an industrial project involves several steps:
- Define project objectives and scope.
- Conduct feasibility studies (e.g., technical, financial aspects).
- Design the project.
- Develop a project plan (e.g., timeline, budget).
- Obtain required permits and approvals.
- Procure materials and resources.
- Execute construction.
- Monitor project progress and manage challenges.
- Commission and handover of the completed facility.
What are quality management practices in the construction industry?
Quality management practices in the construction industry include:
- Training staff on quality standards.
- Enforcing quality control for standards compliance.
- Conducting regular inspections to address quality issues.
- Documenting processes with quality management systems.
What are the current issues in Malaysia’s construction industry?
Current issues in the construction industry in Malaysia may include:
- Labor shortages and skills gaps
- Regulatory challenges
- Fluctuating material prices
- Environmental sustainability concerns
- Technological advancements
- Safety issues on construction sites
Partner with SJEC, an industry expert experienced in navigating the challenges of Malaysia’s construction landscape.
What is SJEC’s stand on sustainability practices for construction projects?
SJEC is committed to incorporating eco-friendly practices into our industrial construction projects. By using sustainable solutions, we minimize environmental impact while ensuring smooth and efficient operations.
What type of industrial construction services does SJEC offer?
SJEC offers warehouse construction, material storage shed construction, industrial equipment installation service, and production line installation service.
What is the range of industrial construction services that SJEC offers?
SJEC provides expertise across the entire spectrum: from design and engineering to procurement, fabrication, constriction, and commissioning (EPCC) of industrial plants and production systems.
References
- https://edition.cnn.com/2018/05/04/asia/hong-kong-zhuhai-macau-bridge/index.html&lang=en
- https://www.getpowerplay.in/resources/blogs/construction-processes-industry-best-practices
- https://www.fieldwire.com/blog/four-steps-for-more-sustainable-construction-management/
- https://macaonews.org/news/greater-bay-area/hong-kong-zhuhai-macao-bridge-five/
- https://skyscraper.org/programs/world-one-and-the-world-towers-mumbai/
- https://www.sciencetimes.com/articles/30881/20210427/fleet-3-000-robots-working-ocados-automated-warehouse-making-online.htm
- https://www.g2.com/articles/warehouse-automation-statistics
- https://www.bimspot.io/blogs/how-does-bim-save-money/
- https://www.weforum.org/agenda/2021/02/why-the-buildings-of-the-future-are-key-to-an-efficient-energy-ecosystem/
- https://www.british-assessment.co.uk/insights/the-cost-benefits-of-sustainable-buildings-and-construction/